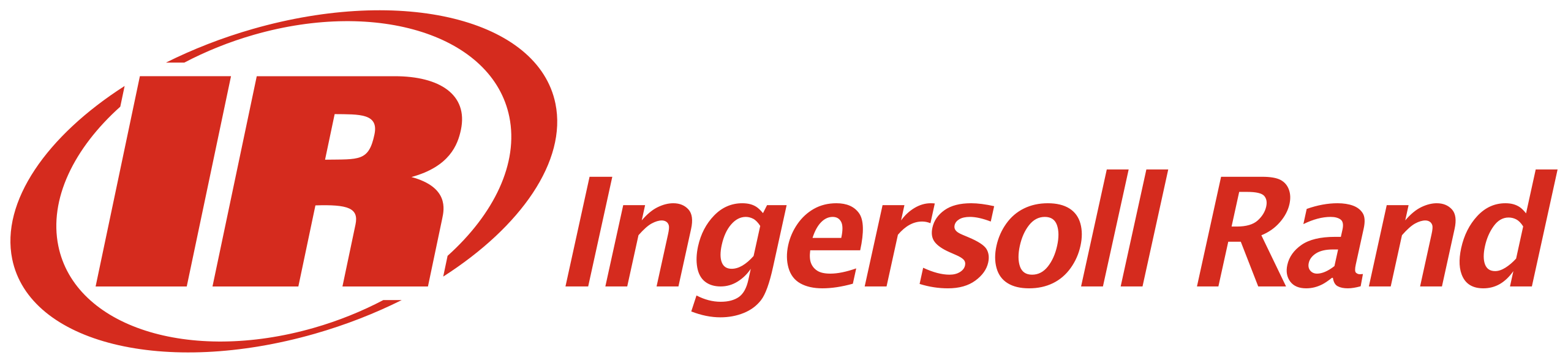
SPXFLOW ATS is now acquired by IR Ingersoll Rand
ATS (Air Treatment Solutions)
Ingersoll Rand is a global market leader with a broad range of innovative and mission-critical air, fluid, energy and medical technologies, providing services and solutions to increase industrial productivity and efficiency. Since merging with Gardner Denver in early 2020, we have more than 300 years of combined experience and innovative expertise.
-
Heatless regenerative dryers.
-
Heat reactivated dryers.
-
Special gas dryers.
-
Desiccant and activated alumina.
-
Air and gas dryers upgrade and retrofit.
-
Air filters and automatic drains.